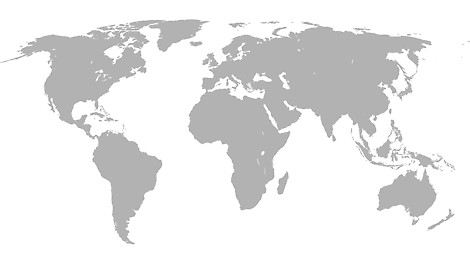
More about PERI
Understand more about us and how the history of PERI can help solve your challenges on the construction site now and in the future
We have a proud history of success and growth, but the challenge never stops. We will evolve to meet the changes in our industry to best support our customers for the long term. A snapshot of our business today shows our global reach and experiences can be used to solve your local challenges:
Understand more about us and how the history of PERI can help solve your challenges on the construction site now and in the future
The issue of sustainability is at the heart of our business processes. Our product development is already focused on the best utilisation of materials and their most economical use.
Raw material selection and procurement is carried out in terms of ecological sustainability, with timber for example coming mainly from certified growing regions.
New technologies and efficient production processes ensure the best quality products with long service life which in turn has a positive effect on the consumption of natural resources.
Delivery and construction site logistics are also optimised regarding shipping volumes and transportation routes.
Strategically-positioned depots and facilities guarantee short delivery distances, and transport is also continuously optimised through an intelligent logistics network. We are also employing an ever-increasing range of sustainable energy sources for our facilities, including biomass and solar energy generation.
Our Sustainability Report provides further information on how we approach the topic of sustainability at PERI.
We report openly and transparently on where we stand today, in which areas we can and must improve and which concrete sustainability goals PERI has set itself for the medium and long term.